top of page
Spindle
3.
Spindle
Spindle-gear
Benefits:
1. Driveline torsional rigidity, can withstand low speed and high torque loads.
2. Suitable for low speed and heavy cutting , but the spindle rigidity to be increased.
3200rpm ~ 5200rpm used helical gear
6000rpm ~ 8000rpm used spur gears.

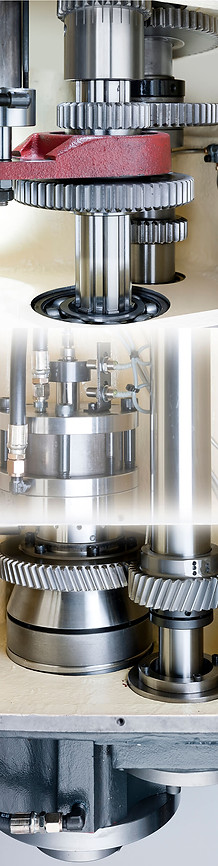
Direct-drive spindle produces doesn’t not have vibration problems, and can improve the surface roughness and accuracy of the workpiece. With oil and gas (Oil-Air) lubrication design, which can effectively be cooled and compressed air is introduced to the oil continuing to increase bearing life, high-speed spindle design used.
Benefits:
1. The high-speed, noise far below the belt spindle.
2. Direct electromagnetic energy - mechanical energy conversion.
3. Low transmission power loss.
4. The low-speed heavy cutting of the trip does not have a belt-type problem.
5. Optimum symmetrically designed spindle head.
6. The entire headstock assembly is counter balanced by dual hydraulic cylinder.
Application area are to automobile mold, plastic injection mold, die-casting mold high speed machining.
Spindle-direct drive
Spindle-built in
Built-in spindle that is the spindle motor and spindle combined, will be installed with the spindle motor rotor spindle, motor stator mounted within the quill, its operating principle
And generally the same spindle motor, has a simple structure, light weight, low inertia, etc., and high-speed, power, accuracy and low vibration characteristics.
Benefits:
Direct transmission of electromagnetic energy into mechanical energy, no transfer of power loss.
In addition, two dual-coil motor having a power output with low speed high torque capabilities.
Low-speed heavy cutting capacity of approximately between gear and belt type; speed cutting ability is better
※Built-in spindle can decrease vibration and get better accuracy when spindle high speed transmission, improve the cutting mark.
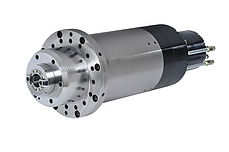
4.
Technical Center
All key components are processed by KAO MING own machining plant in order to control the key technology, accuracy and lead time. The casting and welding components such as bed and column, etc. have to take eliminate stress a long time vibration to eliminate stress and ensure the reliability and stability for the components. Besides, when components are finished, it has to inspect by QA Department firstly to determine whether the dimensions, tolerance, geometric precision of components reaches the standard or not, then can proceed to assemble stage.
During assembly, the connected and sliding surfaces have to be scrapped by technicians with experiences more than 20 years. The guide way which is done by heat treatment to make the guide way harder and the full travel supporter design with high rigidity to assemble the high accuracy & perfect machines.

Technical Center


CTSP
No.53, Houke S. Rd,. Houli Dist, Taichung City 421012, Taiwan
TEL / +886-4-2557-7650
E-MAIL / km@kaoming.com.tw
FAX / +886-4-2557-7630


bottom of page